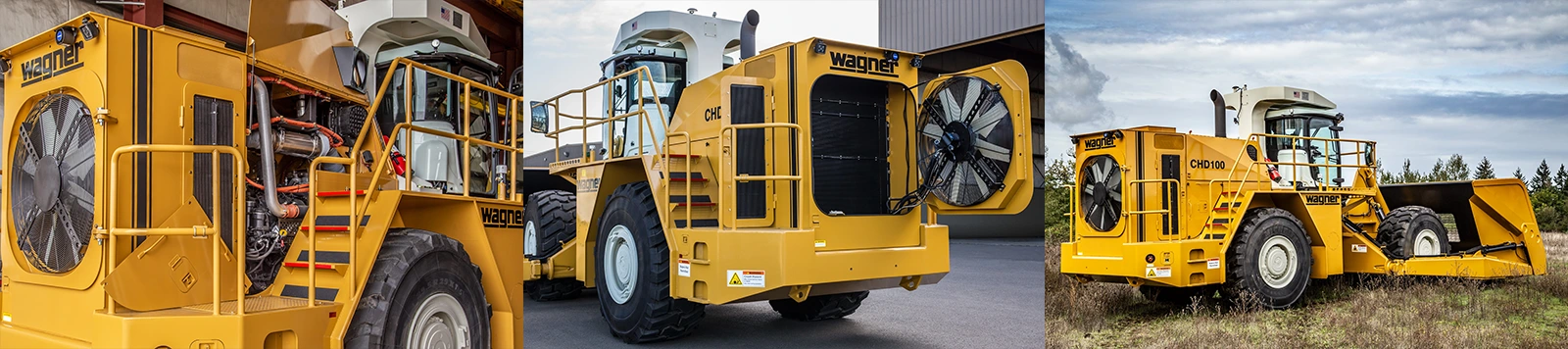
Over the past 50 years, Wagner Chipdozers have been known for their rugged durability. The New Generation Wagner Chipdozers continue that reputation and are the finest and most modern Purpose Built Chip Handling dozer in the industry.
All Wagner Chipdozers come standard with 15 degrees of rear frame oscillation in both directions, keeping the bucket level, even when traveling over uneven ground. It also provides a more comfortable and safer ride for the operator.


Push and Carry More At Once
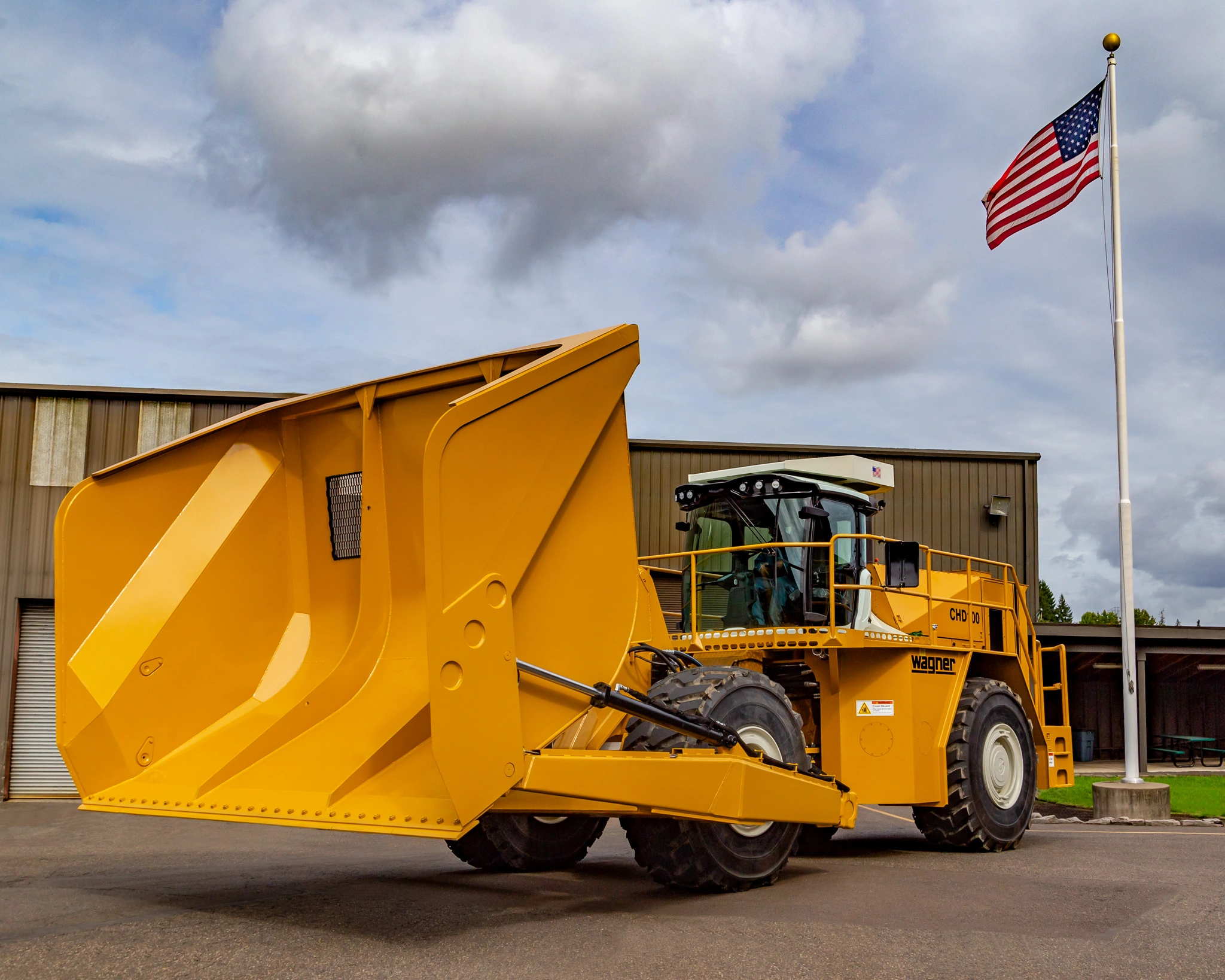
Push and Carry means that the bucket holds 50% of the load while dozing an equal amount in front of the bucket. In fact, as the bucket is filled with chips, the weight is transferred through the push frame and chassis and distributed equally to all four wheels maximizing dozing force and compaction.
It also means Wagner Chipdozers do not need to be as heavy as competitor machines so Wagner dozers are using more of their horsepower to push chips and not the machine itself.
Wagner Chip Dozers can push and carry large loads of chips, sawdust, hogfuel, or other woody biomass materials up to 100 cubic yards per pass.
Spacious Cab Provides Improved Comfort
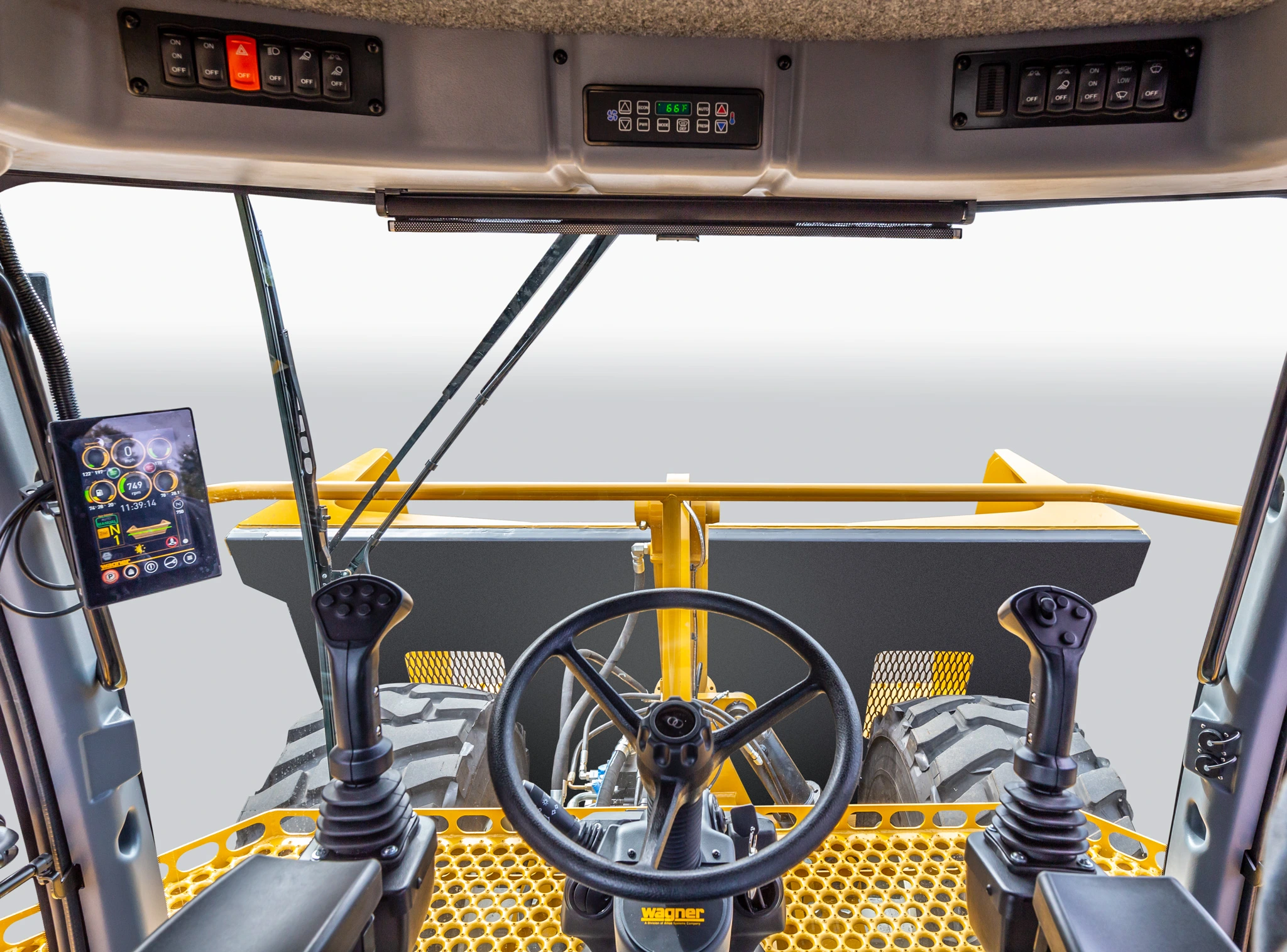
The cab includes a comfortable air ride seat and suspension and comes with a standard full-size trainer seat with adjustable seat belt. Joystick controls are all electric over hydraulic allowing precise control of all functions including steering. The spacious cab includes climate control and has doors on both sides for safety and ease of entry and exit.
All New Generation Chipdozers include the Wagner Smart Screen Operator Interface that replaces the old analog gauges with an easy to read flat panel screen that includes all the key machine parameters. The Smart Screen also allows the operator to start and stop the machine, release or apply the parking brake, and it includes extensive troubleshooting and diagnostic functionality.
Photo shown with optional Steering Wheel.
New Cab Increases Operator Safety

The new and improved cab has more glass that allows for nearly 360 degrees of visibility with minimal blind spots. And screened cut-outs in the bucket provide a clear view to the cutting edges.
The newly-designed tapered ROPS structure protects the operator in case of rollover and minimizes any loss of rear visibility. The walkaround platform is unencumbered and provides safe and easy access to the front of the cab and around both sides of the machine.
The optional manually-activated Fire Suppression system can be applied from inside the cab or at ground level. An automatic fire detection/activation system is also available.
Higher Compaction, Minimal Chip Damage.
As the bucket fills, the weight is transferred evenly through the H-frame and chassis allowing the load to be equally distributed to all wheels for maximum compaction. Wagner Chip Dozers provide 60-70 psi of ground pressure which provides significantly greater compaction than a track machine so customers can store more chips in less space..
Double Reduction Planetary Axles
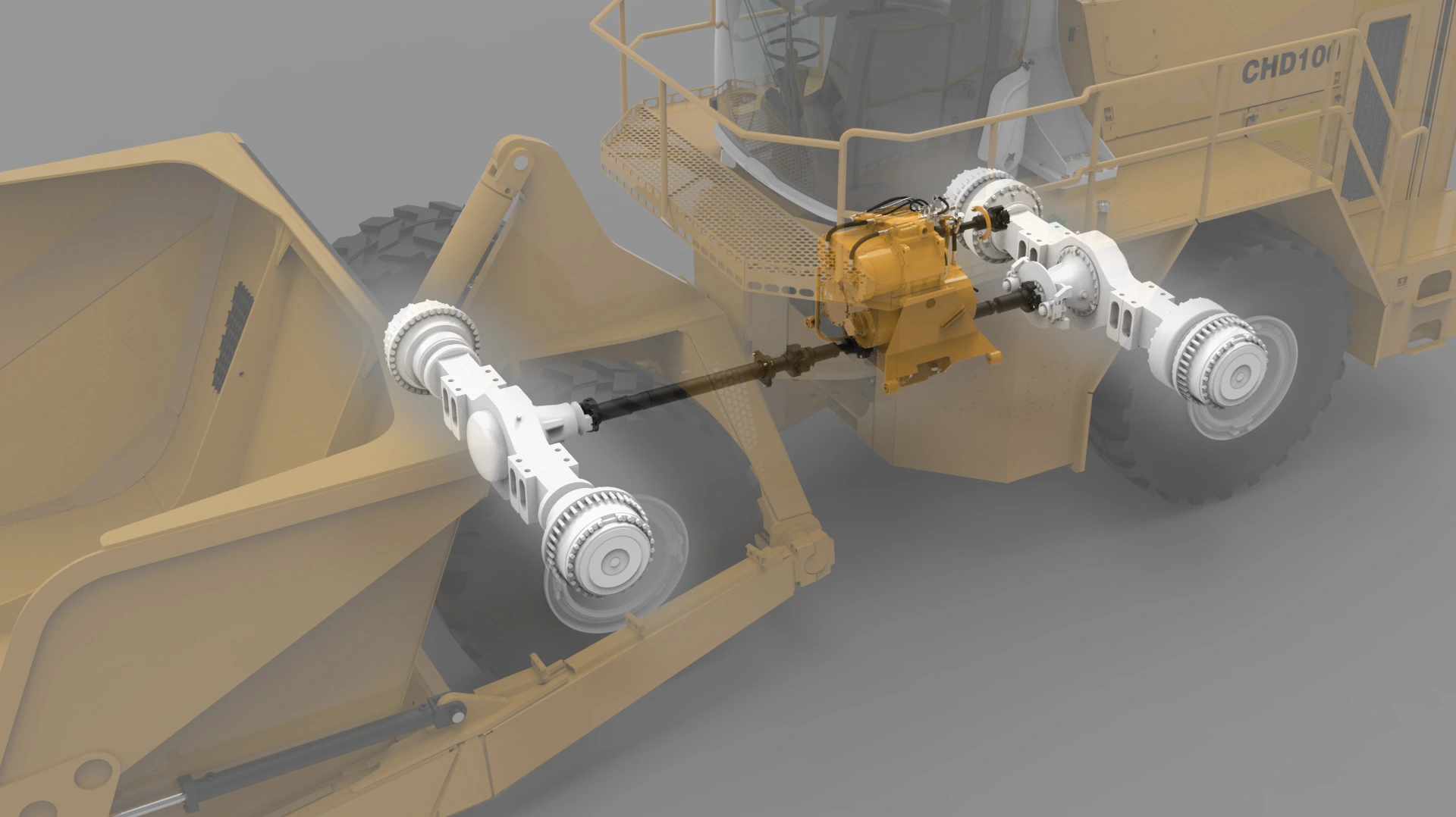
By reducing contact and bending stresses on the gears, the double planetary design ensures longer lasting components.
Better Fuel Economy
Because of the even weight distribution, the engine requires less power to move the entire load, allowing for more work to be done on a single tank of fuel.
Use the calculator to the right to see how much you can save on fuel costs by upgrading to a Wagner CHD100 Chipdozer.
Robust Cooling Package
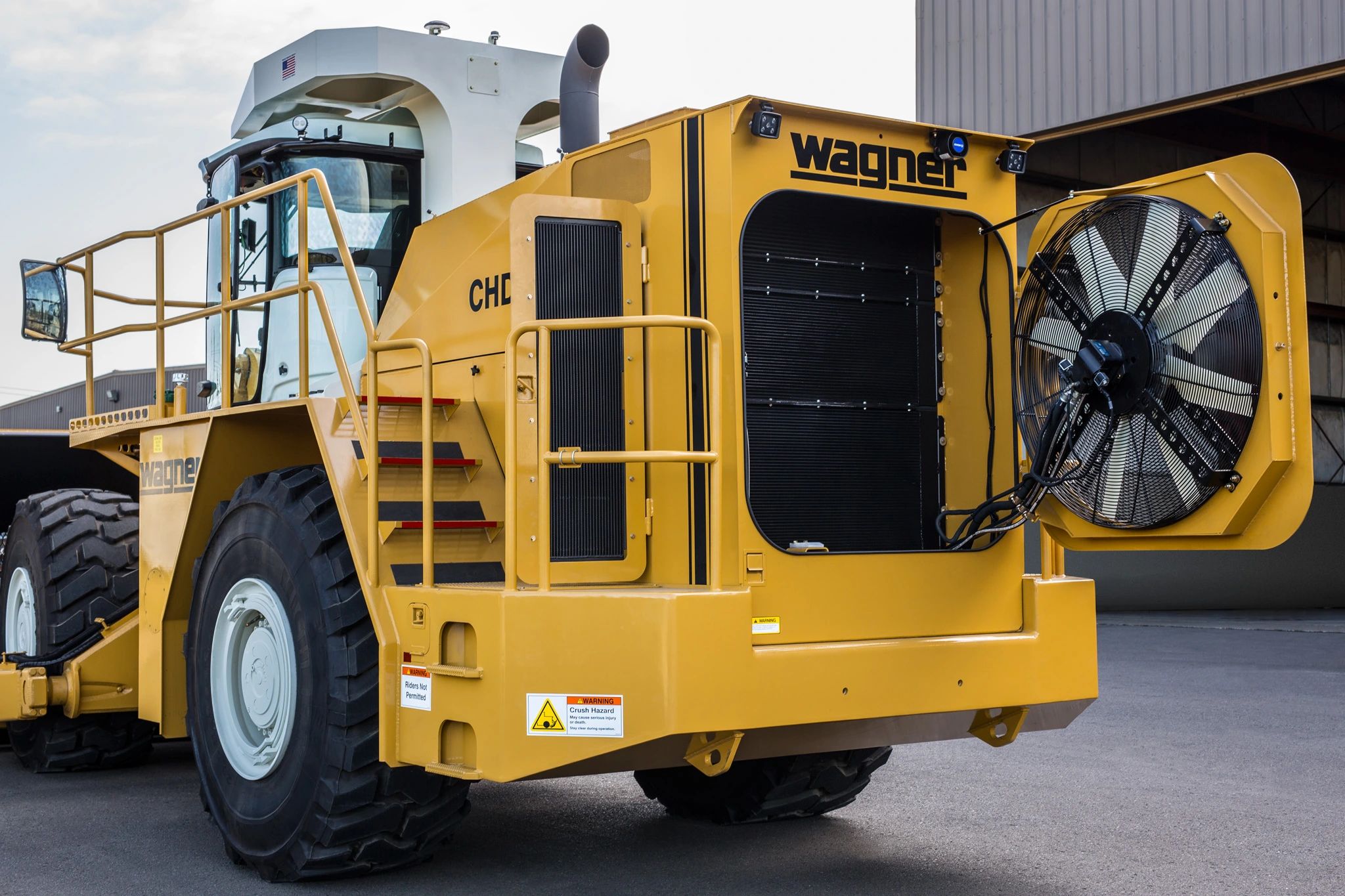
Wagner engineers have completely redesigned the Cooling package to accommodate the Load Sense Hydraulics and Wet Brake. These coolers are mounted behind easy to access bay doors on both sides of the machine and in the rear of the dozer behind a reversible cooling fan. On top of that, the individually replaceable cores make maintenance easy and less costly.
Click to see the Wagner Video Library.
Click here to request more information.
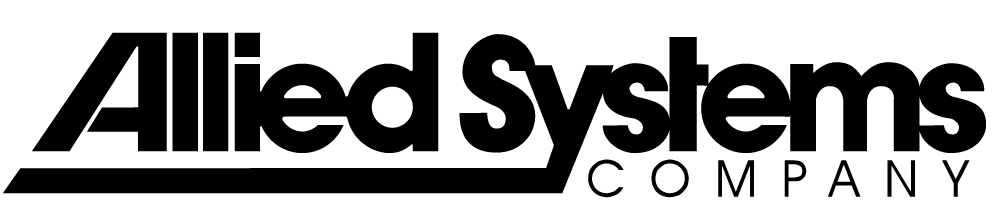
- About Us